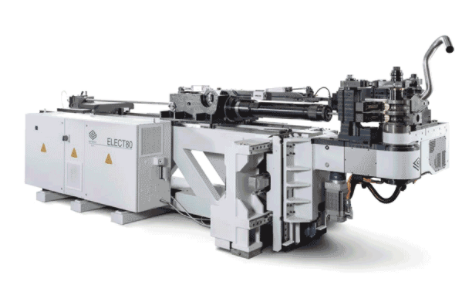
About this Page
This page describes the setup and use of the VTube to BLM communications.
|
|
The Basics of How It Works
- VTube-LASER RECALLS, MODIFIES, and SAVES data directly in ".BLM" files. A communications link can be setup through a standard Windows network connection.
- The communication is bi-directional to and from the bender. It is possible to RECALL data from the BLM using the .BLM file format.
- The data that is included in the BLM file that the AMOB can read is the BENDER data (Xc axis, Yc Axis, Zc Axis). The data also includes the diameter and the cut length.
- The protocol does not send the RADIUS data. Sending radius data causes the VGP-3D to reset the tools and rebuild all custom commands - so VTube-LASER avoids sending this data.
|
|
Communications Setup at the BLM Bender
- Connect the BLM bender to the network using a standard Ethernet cable.
- Setup a shared network location either in the BLM windows control or in a network path on your network.
- If you share a folder on the BLM control, then create a user with a username and password that can be used to login to the computer from the VTube-LASER computer.
|
|
Setup Benderlink at VTube-STEP or VTube-LASER
Entering Benderlink Setup
- Enter the VTube System Options menu.
- Enter the Measure 2 tab menu.
- Enter the Setup Benderlink Network menu.
|
|
Setup the Benderlink Network Grid for the BLM Bender
- Choose an unused row in the grid for a new BLM bender setup. (Click on the image at the right to see a zoomed image.)
- Assign a bender name that will help operators identify what this bender is. This text will be displayed at the top of the Bender Setup menu.
- Set the protocol to BLM Data.
- Enter the path to the shared drive or folder in the NetPath field. Use the same location as the BLM setup. VTube accepts UNC names as well as regular paths with drive letters.
- Enter the IP address in the PING IP ADDRESS field if it is a fixed field. (This is not required. It allows VTube to ping the address to see if the network location is active before trying to open communications.)
- Most BLM benders handle Positive rotations as Clockwise, so you will probably have to enter "YES" for this option (so that the rotations are not corrected backwards).
- Press Close to save the settings. VTube will save these values to a persistent configuration file that will not change unless you change them in this grid.
|
|
How to SEND CORRECTION Data to the BLM Control from VTube-LASER
After Bending the Tube
Bend a tube then measure it with VTube-LASER.
Measure the tube with VTube-LASER
Measure and align the tube to determine if it qualifies by falling within the envelope tolerance for the tube shape.
In the VTube-LASER screen shot, you see the actual result of the first tube not qualifying in shape. The red cells in the tangent point grid on the lower left show that the measured tube centerline is out-of-tolerance.
|
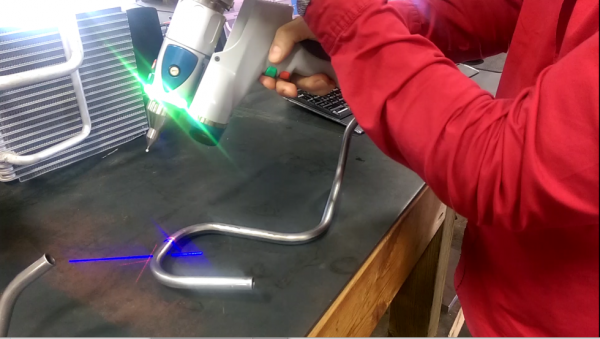

|
Correct the BLM with VTube-LASER - Enter BENDER SETUP
Follow these steps in the VTube-LASER:
Press the "BENDER SETUP button in the Navigation Pane.
|
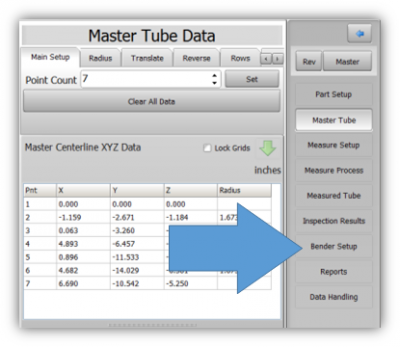
|
INITIAL Setup of Bender Setup Window
The first time in this window for a new part will require these steps before you can correct the BLM bender.
STEP 1 - Set the correct bender number at the top of the window. The BLM bender should display if you have already setup the bender protocol in the Benderlink grid.
STEP 2 - Click on the "Setup This Window" button.
STEP 3 - Click on the "Copy Master LRA to Setup LRA" button.
|
|
Check the BLUE COLUMN Data
The LRA blue column data is now filled with the MASTER LRA data.
This data MUST match the X axis, Y axis, Z axis bender data at the bender - or the corrections will be incorrect.
|
|
(Or in place of Initial Setup) RECALL the Bender Setup from the BLM File
If you have data programmed in the BLM control, then you can also LOAD the current setup data from the BLM file at the control.
STEP 1 - Click on Bidirectional Communication
STEP 2 - Click on AUTO RECALL.
STEP 3 - Load the data from BLM file to the network location.
|

|
Send the Corrections to the BLM File
Save the Correction data to the file for the AMOB to import.
STEP 1 - Click on Bidirectional Communication
STEP 2 - Click on AUTO SEND.
STEP 3 - Save the new VTL file to the network location.
|

|
Import the Correction Data at the AMOB Control
Save the Correction data to the file for the AMOB to import.
STEP 1 - Enter the Program Machine Configuration menu.
STEP 2 - Press the FARO (or it may be "VTube") button
STEP 3 - Open the VTL file.
|

|
AMOB Control Bender Data Updated
The bender data will be updated with the new values.
Bend the corrected part.
|
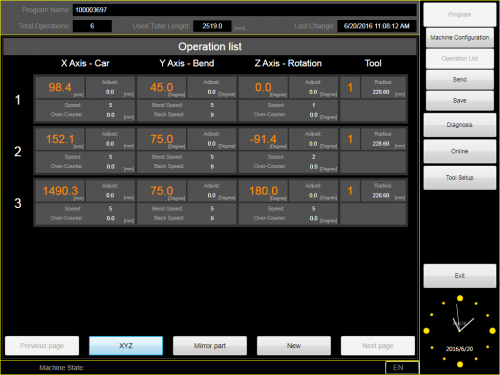
|
Synchronizing the VTube-LASER and AMOB Data Before Corrections
It is critical to be sure the blue columns contain the same data that the AMOB X Axis, Y Axis, Z axis values have before correction is applied.
To make the data the value the same for the next correction, you can press the bottom button in the Bidirectional Communications menu on the right. Be sure you do this BEFORE you measure the next corrected part.
The reason for this step is because the AMOB does not allow VTube to RECALL data in order to update the BLUE columns for the next correction. So this process must be performed manually.
The data in the blue and the orange columns will now be identical. You can exit this window and measure the next corrected part.
|


|
Other Pages